When COVID-19 began to make its appearance in the U.S. last spring, the acquisition of personal protective equipment (PPE) was a global challenge. Worldwide demand for both the products and the raw materials needed to create them soon surpassed supply by a significant margin.
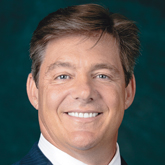
Supply chain professionals across the country came face-to-face with the impact of relying on foreign manufacturers to supply the vast majority of much-needed PPE to protect providers and patients throughout the healthcare community. What had predominantly been a healthcare safety category soon became a household topic. The need for protection went beyond traditional environments and into the general public, further straining the supply chain.
“The pandemic reinforced the need for redundancy and risk mitigation on critical products,” says Ed Jones, President and CEO of HealthTrust. “As an organization, HealthTrust supports increasing manufacturing in the U.S. Establishing domestic mask manufacturing is one critical step, among others, toward creating a more secure PPE supply chain for our membership and community as a whole,” he adds.
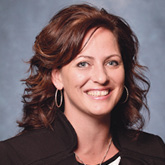
In January of 2020, Rosalind Holloway, Vice President of Global Sourcing at HealthTrust, suggested that HealthTrust explore manufacturing in the U.S. to offset its reliance on sourcing imported masks. This became a major focus for colleagues who were part of the organization’s Manufacturing/New Sources workstream. (See the Q3 article on the 12 pandemic response workstreams initiated by HealthTrust.) Holloway led this workstream, which is composed of colleagues with engineering, manufacturing and product backgrounds. Jones explains, “A thorough understanding of product specifications was part of the critical thinking and methodical evaluation processes used to narrow the field to a short list of quality suppliers. Insight from the Clinical Operations and Global Sourcing teams was paramount to shortening the learning curve, enabling us to move quickly.”
The workstream vetted 50 to 60 companies as potential supply partners and assessed over 40 sites as possible manufacturing locations.
One source that stood out was a global manufacturer with over 30 years of healthcare experience and know-how in producing high-quality products, looking to grow its presence on U.S. soil. Excited by the opportunity to increase long-term mask production in the U.S. for all healthcare providers, HCA Healthcare and the company agreed to launch a manufacturing joint venture to produce level 1 and 3 masks in the U.S.
“The partnership provides an additional supply option to the market without disrupting current supply sources. As needs arise, we will continue to support the evaluation of other products that might become part of this manufacturing partnership,” Jones says.
“HealthTrust values diversification of PPE manufacturing. This joint venture is one way to mitigate risk and create a more stable supply chain while still maintaining valued supplier relationships already in place,” he adds.
Searching for the right joint-venture partner involves a number of important considerations. Some of those include:
- Balance between security of supply and economic viability of supply chain costs
- Vertical integration of raw materials to finish goods; many companies are still sourcing raw materials outside of the U.S.
- Relevant healthcare experience and an understanding of the high-quality product standards required by healthcare providers
- Appropriate balance between redundancy and risk
- Compliance with all applicable FDA standards and other legal and regulatory requirements